Your service center
The waiting time offered by manufacturers for materials requiring multi-stage processing is often unsatisfactory for our customers, especially in the case of sudden/urgent needs. Our cutting machines and an extensive network of subcontractors allow us to perform additional processing on rolled bars that we have in stock.
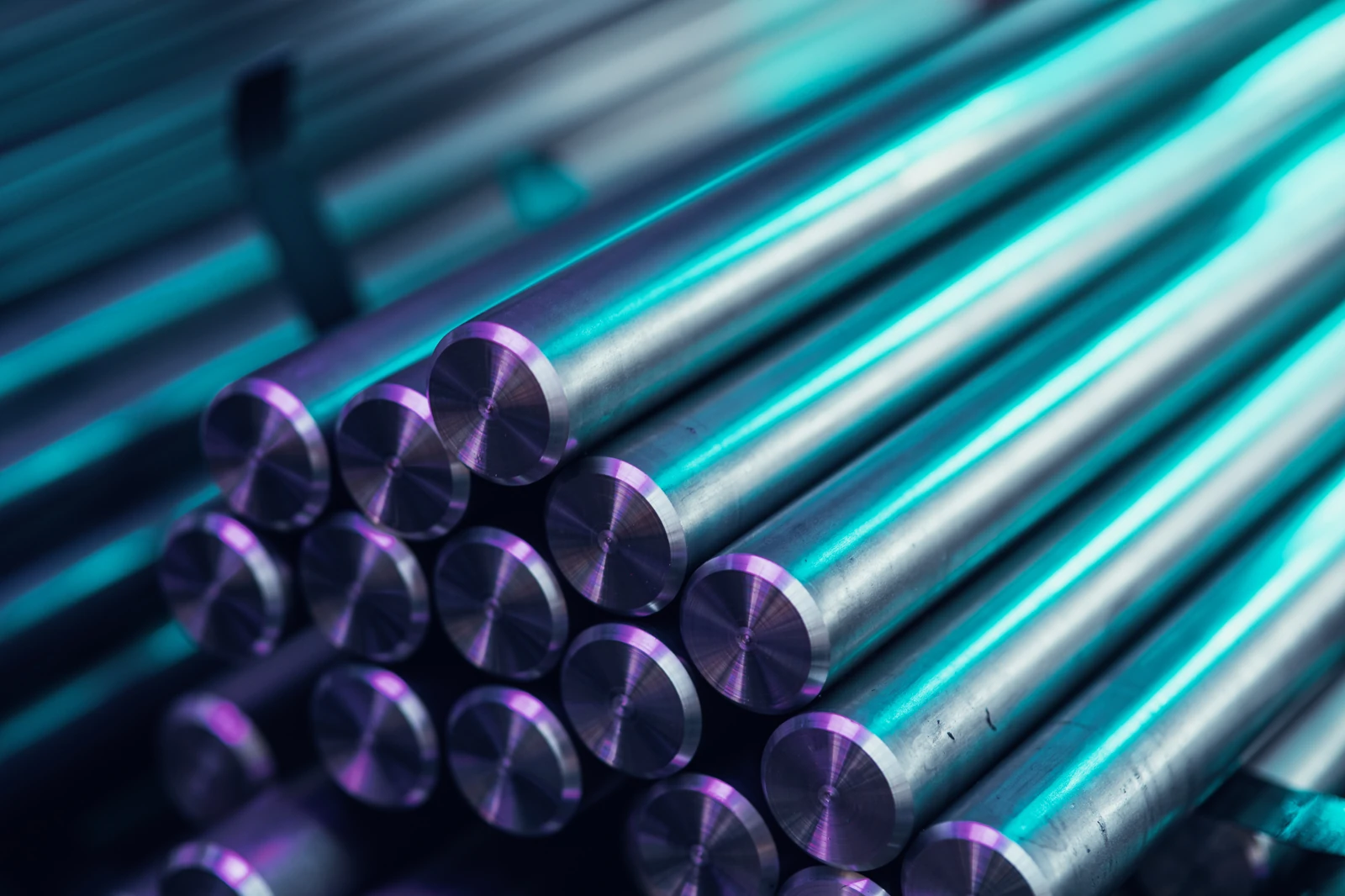
At the customer's request, we can deliver goods with a 3.2 certificate in cooperation with numerous classification societies.
Heat treatment
Normalizing annealing (+N) heat treatment that reduces internal stresses and improves the structure and mechanical properties of the material. At first, the steel is heated to the correct temperature, held at the temperature for a certain amount of time, and then slowly cooled. Normalizing annealing helps in the uniform distribution of alloying elements in the steel structure, eliminates microstructural phenomena and improves its strength and resistance to cracking.
Tempering (+QT) is a process used to improve the mechanical properties of steels or alloys. The "+QT" designation means that the material has undergone a hardening and tempering process. It consists of two main stages. The first stage is quenching, i.e. rapid cooling of the material, usually in oil, water or air. This leads to the formation of hard crystalline structures in the material. The second stage is tempering, where the material is heated to a moderate temperature and then slowly cooled. This process reduces internal stresses and increases the ductility of the material while maintaining an appropriate level of hardness.
Soft annealing (+A) heat treatment used to soften the steel and improve its ductility. It consists in heating the steel to the appropriate temperature, keeping it at this temperature for a certain period of time, and then cooling it in a controlled way. Soft annealing aims to reduce the hardness and internal tensions in the material and improve its deformation properties. During soft annealing, the structure of the steel is recrystallized, resulting in a fine-grained and homogeneous structure. This eliminates the previous microstructures and dissolves the components that make up the network structure. It contributes to a reduction in hardness and an increase in plasticity of the material. Soft annealing can be used after previous quenching or other heat treatment processes to mitigate the effects of hardness and brittleness.
Spheroidizing annealing (+AC) is a process used to obtain spherical graphite carbides in steel. The process is particularly used in cast iron and alloy steels that contain carbon in the form of graphite. In spheroidizing, the steel is heated to a suitable temperature, held at that temperature for a period of time, and then gradually cooled. This process aims to change the structure of the carbide in the steel from lamellar to spherical. As a result, graphite becomes more resistant to cracking and damage, which translates into increased plasticity and strength of steel.
Cold treatment
Forming in which the steel is pulled by special tools to reduce its cross-section and increase its length. This process is often used to produce smaller wire, rods or tubes. In steel drawing, the material is pulled through conical or cylindrical dies while applying pressure.
Peeling involves removing the top layer of steel using specialized cutting tools. This helps to obtain a surface free from discontinuities and to achieve dimensions with very accurate tolerances.
Machining of metal surfaces where grinding tools are used to obtain a smooth, even and precise surface. In grinding, grinding tools such as grinding wheels, sandpaper or grinding stones are used to abrade or remove excess material from the metal surface. This process allows to improve the appearance, eliminate burrs, remove unevenness or improve the dimensional accuracy of metal elements.
The process of mechanically removing material from the inside of an object to create a hole of the desired shape and dimensions. This process is performed using a drill or drilling machine. In hollowing, the drill bit is driven into the metal being worked and then rotated to remove material and create a hole. The rotational speed of the drill bit and the appropriate application of pressure are crucial for efficient and precise drilling.
Technical acceptance
During the commissioning of ABS, various evaluation criteria are used, such as appearance, dimensions, mechanical properties (e.g. strength, flexibility), chemical resistance, thermal stability, etc. All these parameters are compared with specific standards or technical specifications to determine whether products meet quality requirements.
Quality control procedure carried out by Det Norske Veritas (DNV), a renowned international certification organization, in order to assess and confirm the compliance of products, processes or systems with specific norms, standards or technical requirements.
Germanischer Lloyd (GL) specializes in services related to the class of ships, certification of marine technical equipment, maritime safety, offshore wind energy and other aspects of the maritime industry. Technical acceptance of GL is an important stage in the certification and conformity assessment process, which confirms the fulfillment of technical requirements and standards for products or systems.
The TUV (Technischer Überwachungsverein) procedure includes the assessment and confirmation of the conformity of products, processes or systems with specific norms, standards or technical requirements. TUV covers various industry sectors such as automotive, energy, chemical industry, electronics, medicine and many others.
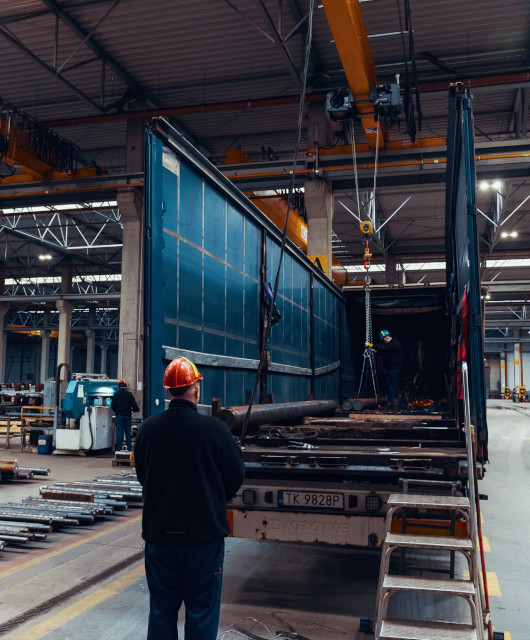
Transport
We do our best to ensure the shortest delivery time as part of our transport services, which is why we carefully select partners who are able to meet our high standards. Our company, FPG, focuses primarily on the proper protection of transported materials and timely delivery of products ordered by the customer. We work with both reputable transport companies and independent carriers to provide our clients with excellent service quality and cooperation at every stage of the transport process.
1 - 5 business days, on popular destinations, throughout Poland
1 - 10 business days, in less frequented directions, throughout Poland
Write to us!
- +48 22 667 94 43
- kontakt@fpg.com.pl
- Office
- 02-495 Warszawa, pl. Czerwca 1976 r. nr 2
- Warehouse
- 05-170 Zakroczym, ul. Stalowa 11